Centered Flow
In comparison to traditional ‘line of site’ control valves (such as ball valves, butterfly valves and pinch valves), which direct high velocity slurry towards the valve’s body and pipe wall, our patented trim design acts as a variable orifice, centering the abrasive flow. This protects the pressure containing valve body and the integrity of the downstream piping from erosion.
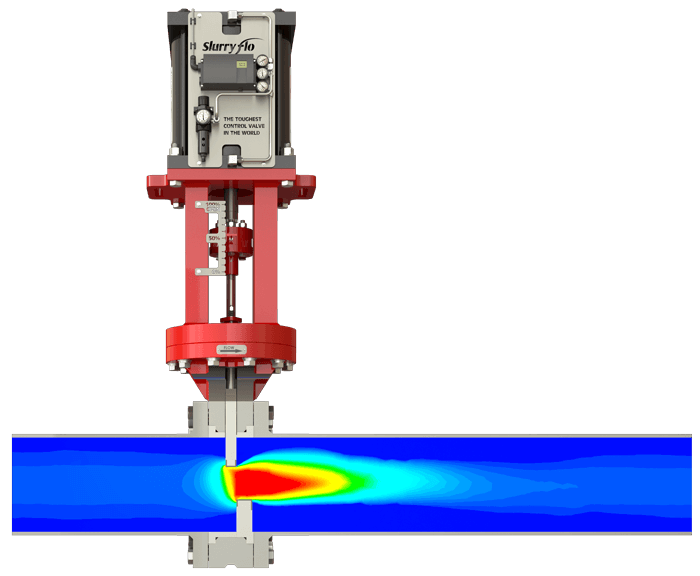