Traditionally, multi-orifice pressure reduction devices, such as globe valves with anti-cavitation trims have been utilized to mitigate cavitation and turbulent flow. In many instances however, control valves with “multi-stage continuous-resistance trims” have a short service life and limited control capacities over a wide range of operating conditions. If scale or slurries are present, the small orifices in these types of trims are prone to erosion and plugging.
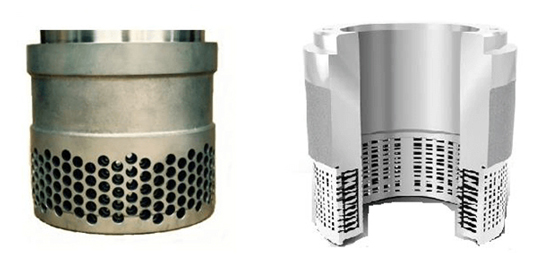
Traditional 'anti-cavitation' control valve trims for pressure reduction.