A client in the gas processing industry had several ANSI 600 SlurryFlo control valves with custom seat plate geometry (see Figure 1). After 18 months of continuous service, a sudden increase in flow rate resulted in the valves becoming a bottleneck in their process. The pressure drop across the valves now restricted the plant’s potential throughput. Based on new flow data, the client estimated the loss in production was +$250,000 per day.
Upon notice of the new flow conditions, SAF engineers designed an alternate custom seat plate for the existing valves (see Figure 2). The new component sufficiently decreased the pressure drop, allowing the client to take full advantage of their new situation. Due to our patented modular trim design, there was no need to replace the entire valve assembly.
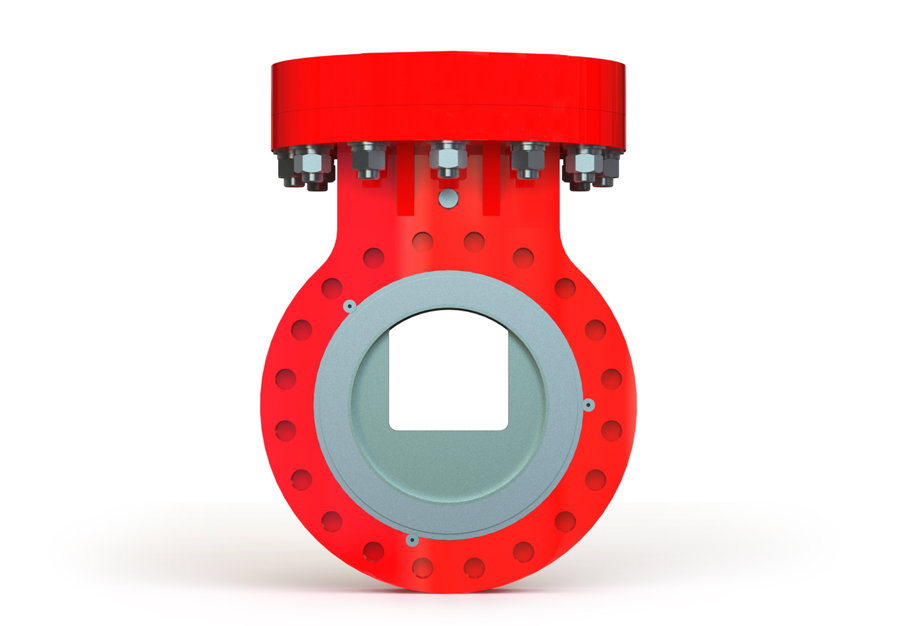
Figure 2
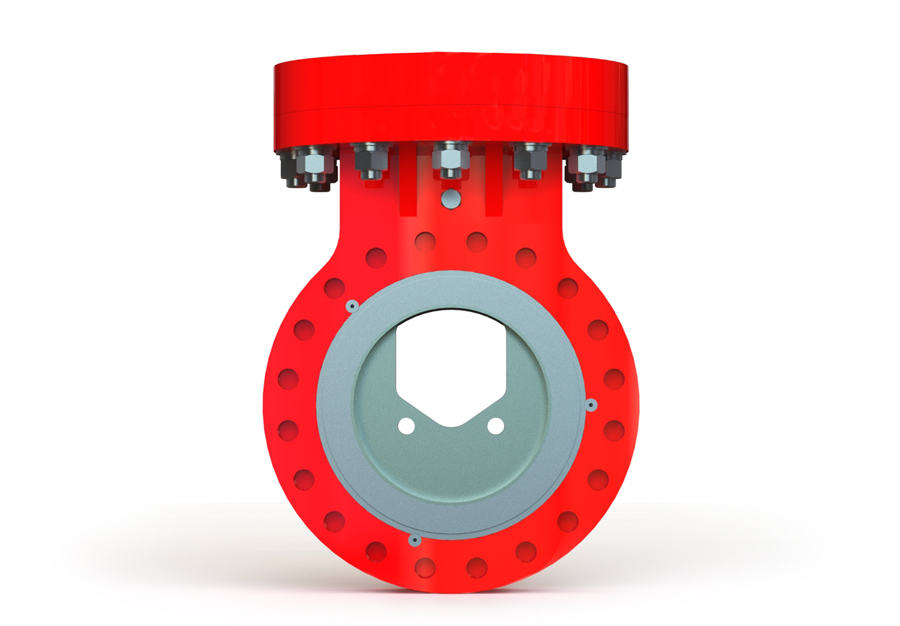
Figure 1